All contaminated disposable sharps generated in a California dental office must be placed into a…
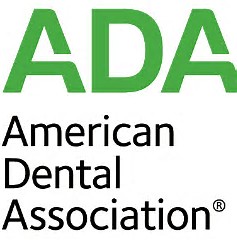
Cleaning is Essential First Step When Reprocessing Dental Instruments
In late 2020, the American Dental Association (ADA) issued the Technical Report Guidance on Method Development and Validation of Cleaning Processes for Dental Instruments to help guide manufacturers of reusable dental instruments on developing and validating reprocessing instructions that follow requirements of the US Food and Drug Administration (FDA).
All reusable dental instruments must be effectively reprocessed after each patient for reuse. According to the US Centers for Disease Control and Prevention (CDC), if instruments are not cleaned before being sterilized, residual debris on the surface can prevent heat or chemical vapor from contacting the surface area, thereby hindering downstream sterilization, leading to potential cross contamination and/or failure of the device. ADA’s Technical Report further states that “if an instrument cannot be cleaned using a validated method, then it should be labeled as single-use and should not be reused”.
Reusable instruments should be cleaned with hands-free, automated cleaning equipment such as an ultrasonic unit. If manual scrubbing is necessary, a long-handled brush should be used to keep hands away from the contaminated sharp instruments. DHCP working in the central processing area should wear chemical-resistant and/or puncture-resistant rubber or plastic gloves when cleaning contaminated instruments and devices. Facemasks, eye protection such as goggles or full-length faceshield, and appropriate protective gowns should be worn when exposure to blood, contaminated fluids, and/or chemicals may occur.
Since 1992, OSHA Review, Inc. has provided dental professionals with comprehensive programs to support regulatory compliance and infection control. We are a registered continuing education provider in the state of California, specializing in Dental Practice Act, infection control, and OSHA training.